
In modern architecture, decoration and furniture making, 12-inch panels are the core material of many projects because of their moderate size and wide range of uses. However, ordinary nails or screws are often not fully qualified for the high-strength fixing requirements of such plates, which can easily lead to loosening or even damage. Therefore, it is particularly important to adopt a professional 12-inch plate fastening solution .
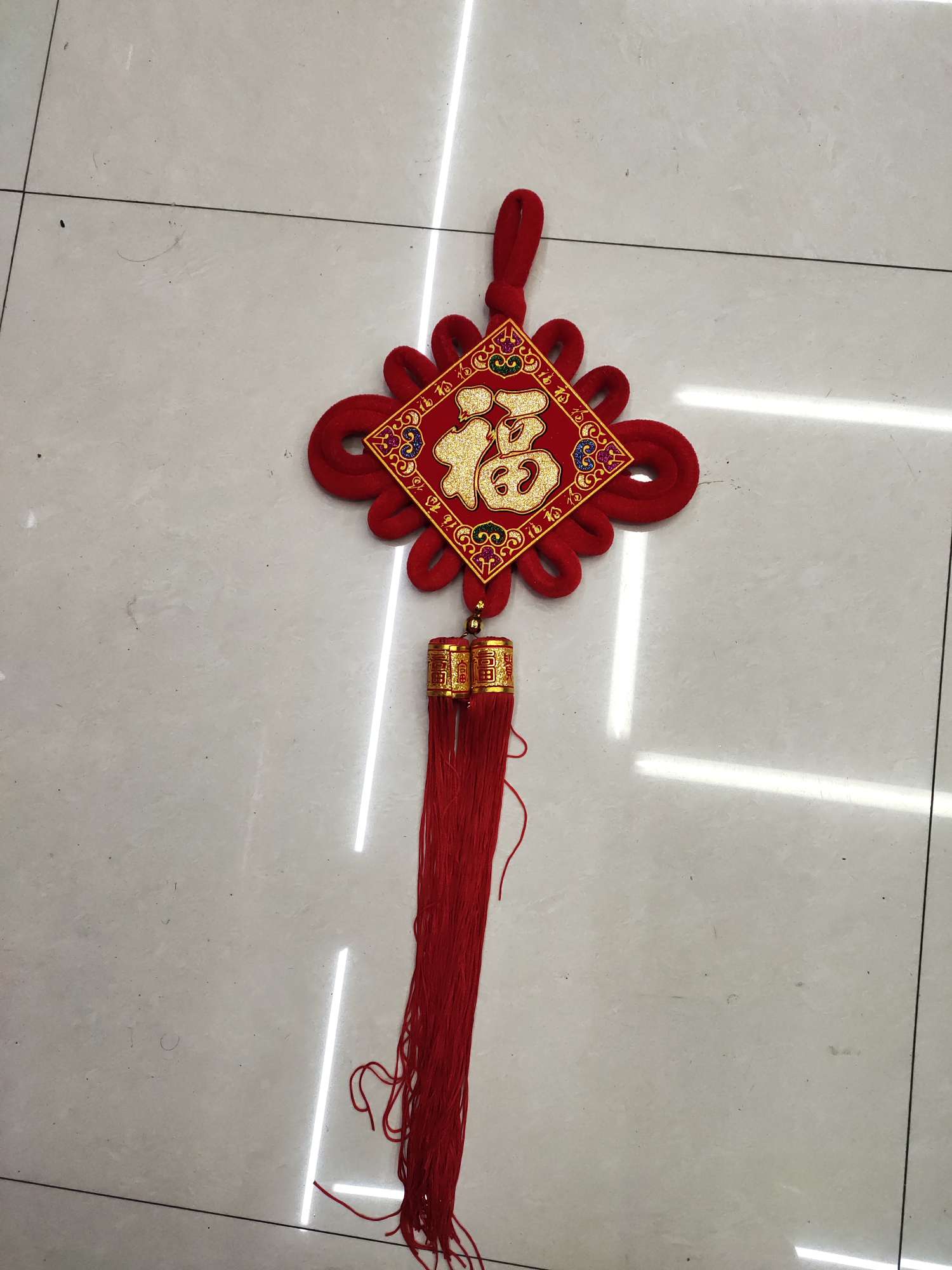
So what makes for such excellent fixing performance? Our fastening systems use the main components made of high quality alloy steel and are precision machined to ensure that every detail is industry-leading. Not only that, the unique surface coating technology not only enhances corrosion resistance, but also ensures its stability in extreme environments.
Although it sounds complicated, the installation process of the system is extremely simple. Just follow the following steps:
first place the special fixture between two 12-inch plates to be fixed; Then use the attached wrench to tighten the tightening nut until you hear a slight "click"-this indicates that the ideal pre-pressure state has been reached; Finally, remove the excess part to complete the whole operation process. No additional tool support is required throughout the process, which greatly improves work efficiency.
The scope of application of this program far exceeds expectations. In the field of home decoration, it can be used to play an important role in the work links such as bookshelf assembly or gap filling and reinforcement in the process of floor laying. On the other hand, on the industrial production line, it is suitable for fast and efficient assembly tasks under various occasions such as mechanical equipment frame construction and large storage shelf splicing.
Let's take a look at how one customer's experience benefited from this innovation! Mr. Zhang is the owner of a small woodworking workshop. In the past, he often encountered the problem of deformation of finished products due to uneven manual percussion. Since the introduction of this fastening device, all processes have become more precise and controllable, and the chance of rework has been significantly reduced, thus saving a lot of cost.
Of course, there are some key elements that need to be understood before choosing the right fastening product. For example, what is the maximum tensile force required to be borne in a specific application scenario? Whether environmental factors will adversely affect its long-term performance and other issues need to be considered in advance before making a decision. In addition, we should also pay attention to check the warranty period and relevant after-sales service terms and other content information provided by the manufacturer so as to make future maintenance more worry-free.
Looking to the future, with the continuous development and progress of science and technology, the trend of intelligent automation is gradually penetrating into various traditional industries. It can be predicted that the future of fastening technology will move towards more accurate and efficient direction, perhaps one day we will see the robot arm automatically complete all the relevant work scene is no longer far away.
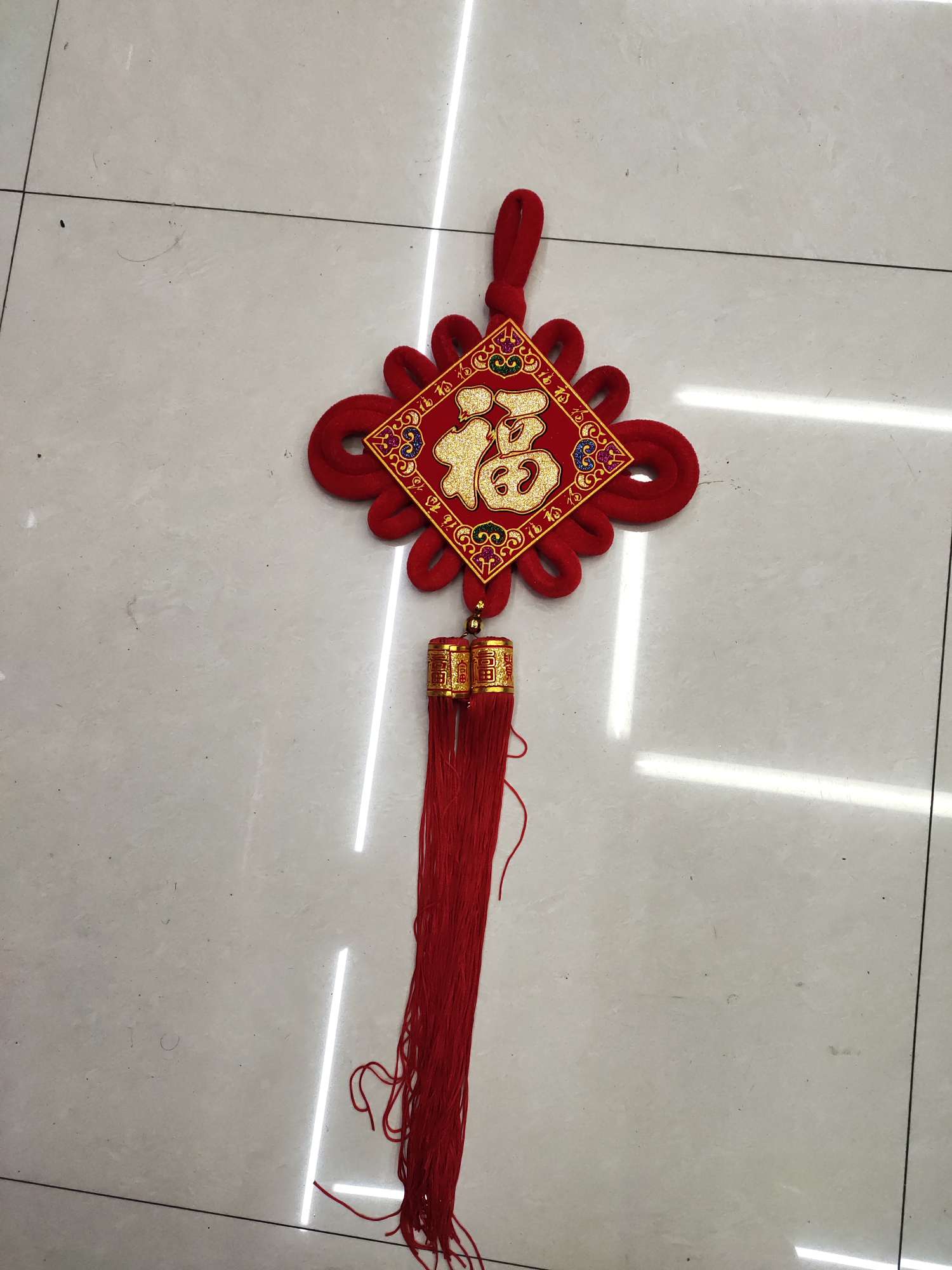